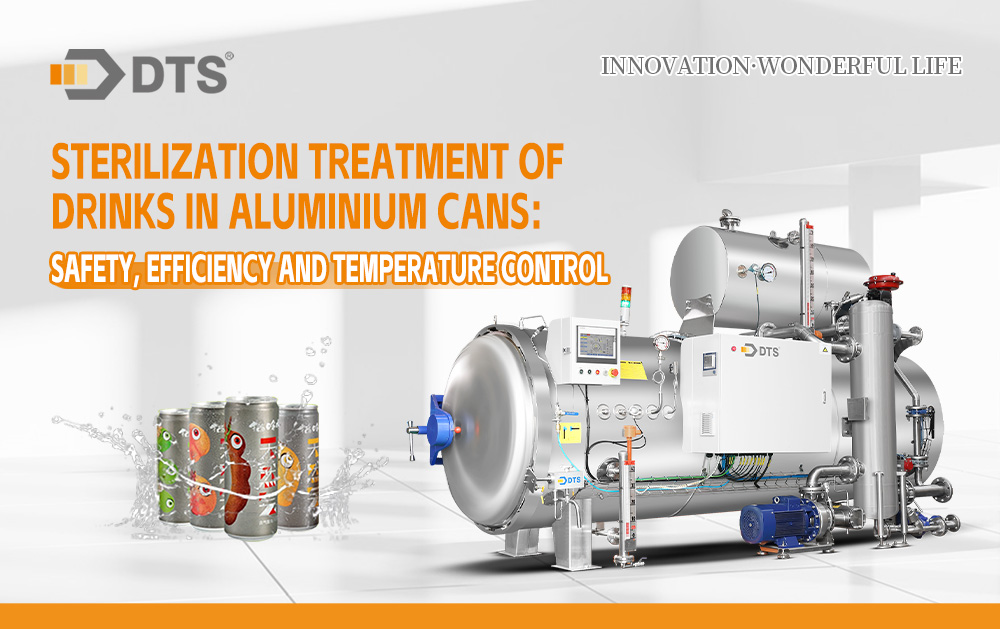
Sterilization is one of the most important aspects of beverage processing, and a stable shelf life can only be obtained after the appropriate sterilization treatment.
Aluminium cans are suitable for top spraying retort. The top of the retort is set up with spraying partition, and the sterilizing water is sprayed down from the top, which penetrates the products in the retort evenly and comprehensively, and ensures the temperature in the retort is even and consistent without dead angle.
The spray retort operation firstly loads the packaged products into the sterilization basket, then sends them into the water spray retort, and finally closes the door of the retort.
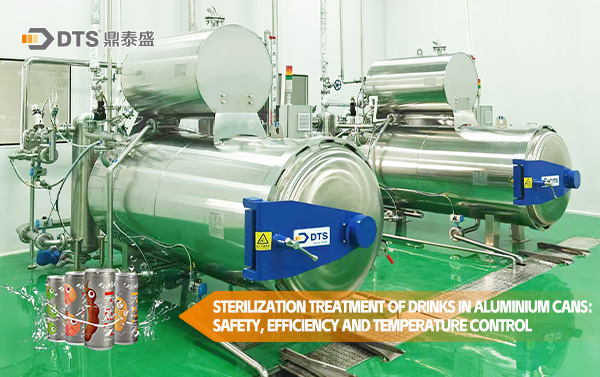
During the whole sterilization process, the retort door is mechanically locked and without door popping open, thus ensuring the safety of people or things around the sterilization. The sterilization process is carried out automatically according to the data entered into the microprocessor controller PLC. Note that an appropriate amount of water should be retained at the bottom of the water spray retort. If required, this water can be automatically injected at the beginning of the temperature rise. For hot-filled products, this part of the water can be first preheated in the hot water tank and then injected. During the whole sterilization process, this part of the water is repeatedly circulated through a high-flow pump to spray-heat the product from top to bottom. The steam passes through another circuit of the heat exchanger and the temperature is adjusted according to the temperature setpoint. The water then flows evenly through the distribution disc at the top of the retort, showering the entire surface of the product from top to bottom. This ensures an even distribution of heat. The water that has been drenched over the product is collected at the bottom of the vessel and flows out after passing through a filter and collection pipe.
Heating and sterilization Stage: Steam is introduced into the primary circuit of the heat exchanger by automatically controlling the valves according to the edited sterilization program. Condensate is automatically discharged from the trap. Since the condensate is not contaminated, it can be transported back to the retort for use. Cooling Stage: Cold water is injected into the initial circuit of the heat exchanger. The cold water is regulated by an automatic valve located at the inlet of the heat exchanger, which is controlled by a program. Since the cooling water does not come into contact with the interior of the vessel, it is not contaminated and can be reused. Throughout the process, the pressure inside the water spray retort is controlled by the program through two automatic angle-seat valves feeding or discharging compressed air into or out of the retort. When the sterilization is finished, an alarm signal is given. At this point the kettle door can be opened and the sterilized product pulled out.
Post time: Oct-24-2024