As everyone knows, the sterilizer is a closed pressure vessel, usually made of stainless steel or carbon steel. In China, there are about 2.3 million pressure vessels in service, among which metal corrosion is particularly prominent, which has become the main obstacle and failure mode affecting the long-term stable operation of pressure vessels. As a kind of pressure vessel, the manufacturing, use, maintenance and inspection of the sterilizer can’t be ignored. Due to the complex corrosion phenomenon and mechanism, the forms and characteristics of metal corrosion are different under the influence of materials, environmental factors and stress states. Next, let's delve into several common pressure vessel corrosion phenomena:
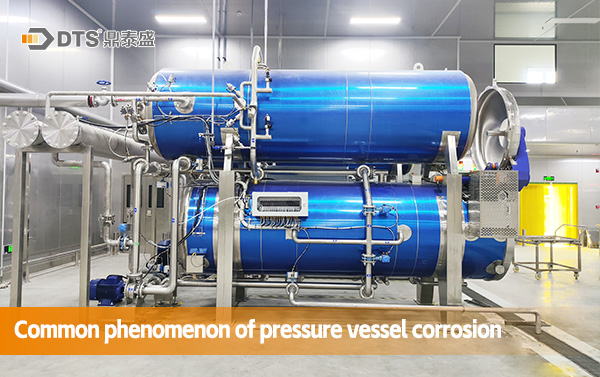
1.Comprehensive corrosion (also known as uniform corrosion), which is a phenomenon caused by chemical corrosion or electrochemical corrosion, the corrosive medium can reach all parts of the metal surface evenly, so that the metal composition and organization are relatively uniform conditions, the entire metal surface is corroded at a similar rate. For stainless steel pressure vessels, in a corrosive environment with low PH value, the passivation film may lose its protective effect due to dissolution, and then comprehensive corrosion occurs. Whether it is a comprehensive corrosion caused by chemical corrosion or electrochemical corrosion, the common feature is that it is difficult to form a protective passivation film on the surface of the material during the corrosion process, and the corrosion products may dissolve in the medium, or form a loose porous oxide, which intensifies the corrosion process. The harm of comprehensive corrosion can’t be underestimated: first, it will lead to a reduction in the pressure area of the pressure vessel bearing element, which may cause perforation leakage, or even rupture or scrap due to insufficient strength; Secondly, in the process of electrochemical comprehensive corrosion, H+ reduction reaction is often accompanied, which may cause the material to be filled with hydrogen, and then lead to hydrogen embrittle and other problems, which is also the reason why the equipment needs to be dehydrogenated during welding maintenance.
2. Pitting is a local corrosion phenomenon that begins on the metal surface and expands internally to form a small hole shaped corrosion pit. In a specific environmental medium, after a period of time, individual etched holes or pitting may appear on the metal surface, and these etched holes will continue to develop to the depth over time. Although the initial metal weight loss may be small, due to the rapid rate of local corrosion, equipment and pipe walls are often perforated, resulting in sudden accidents. It is difficult to inspect pitting corrosion because the pitting hole is small in size and is often covered by corrosion products, so it is difficult to measure and compare the pitting degree quantitatively. Therefore, pitting corrosion can be considered as one of the most destructive and insidious corrosion forms.
3. Intergranular corrosion is a local corrosion phenomenon that occurs along or near the grain boundary, mainly due to the difference between the grain surface and the internal chemical composition, as well as the existence of grain boundary impurities or internal stress. Although intergranular corrosion may not be obvious at the macro level, once it occurs, the strength of the material is lost almost instantaneously, often leading to the sudden failure of the equipment without warning. More seriously, intergranular corrosion is easily transformed into intergranular stress corrosion cracking, which becomes the source of stress corrosion cracking.
4. Gap corrosion is the corrosion phenomenon that occurs in the narrow gap (width is usually between 0.02-0.1mm) formed on the metal surface due to foreign bodies or structural reasons. These gaps need to be narrow enough to allow the fluid to flow in and stall, thus providing the conditions for the gap to corrode. In practical applications, flange joints, nut compaction surfaces, lap joints, weld seams not welded through, cracks, surface pores, welding slag not cleaned and deposited on the metal surface of the scale, impurities, etc., may constitute gaps, resulting in gap corrosion. This form of local corrosion is common and highly destructive, and can damage the integrity of mechanical connections and the tightness of equipment, leading to equipment failure and even destructive accidents. Therefore, the prevention and control of crevice corrosion is very important, and regular equipment maintenance and cleaning are required.
5. Stress corrosion accounts for 49% of the total corrosion types of all containers, which is characterized by the synergistic effect of directional stress and corrosive medium, leading to brittle cracking. This kind of crack can develop not only along the grain boundary, but also through the grain itself. With the deep development of cracks to the interior of the metal, it will lead to a significant decline in the strength of the metal structure, and even make the metal equipment suddenly damaged without warning. Therefore, stress corrosion-induced cracking (SCC) has the characteristics of sudden and strong destructive, once the crack is formed, its expansion rate is very fast and there is no significant warning before the failure, which is a very harmful form of equipment failure.
6. The last common corrosion phenomenon is fatigue corrosion, which refers to the process of gradual damage to the surface of the material until rupture under the combined action of alternating stress and corrosive medium. The combined effect of corrosion and material alternating strain makes the initiation time and cycle times of fatigue cracks shorten obviously, and the crack propagation speed increases, which results in the fatigue limit of metal materials greatly reduced. This phenomenon not only accelerates the early failure of the pressure element of the equipment, but also makes the service life of the pressure vessel designed according to the fatigue criteria much lower than expected. In the process of use, in order to prevent various corrosion phenomena such as fatigue corrosion of stainless steel pressure vessels, the following measures should be taken: every 6 months to thoroughly clean the inside of the sterilization tank, hot water tank and other equipment; If the water hardness is high and the equipment is used more than 8 hours a day, it is cleaned every 3 months.
Post time: Nov-19-2024